What is a ball bearing and how does it work?
- What it is: Think of a ball bearing as a simple device that helps things spin or roll smoothly. Its main job is to reduce friction between moving parts. Imagine trying to drag a heavy box versus rolling it on logs – rolling is much easier! Ball bearings do the same for machine parts.
- How it works: A basic ball bearing has two rings (called races – an inner race and an outer race), a set of small, round balls between the rings, and usually a cage (or retainer) to keep the balls evenly spaced.
- One race is typically attached to the stationary part (like the housing of a motor), and the other is attached to the rotating part (like the shaft).
- As the shaft tries to turn, the balls roll smoothly along the tracks (raceways) on the inner and outer rings.
- This rolling motion creates much less friction than if the two parts were just rubbing directly against each other. This allows parts to move faster, more efficiently, and with less wear and tear.
What are the main types of ball bearings and their characteristics/applications?
- Deep Groove Ball Bearings: Most common and versatile. Good for radial loads (outward force) and some axial loads (sideways force) in both directions. Used in motors, wheels, appliances.
- Angular Contact Ball Bearings: Handle both radial and axial loads simultaneously, especially higher axial loads in one direction. Often used in pairs. Good for high speeds like in machine tools or pumps.
- Self-Aligning Ball Bearings: Can handle slight misalignment between the shaft and housing thanks to their special outer ring shape. Used in farm equipment, fans, conveyors where alignment isn’t perfect.
- Thrust Ball Bearings: Designed only for axial loads (pushing/pulling along the shaft). Cannot handle much radial load. Used in rotating tables or jacks.
In addition, TFL can also provide other types of ball bearings. For more detailed product information, please read our ball bearing catalog.
How do I choose the right ball bearing for my application? What factors to consider?
Factor | Description | Key Considerations |
Loads | Type and magnitude of forces the bearing must handle. | – Radial, axial, or combined loads. – Check static and dynamic load ratings. |
Speed | Rotational speed in RPM. | – Verify limiting speed from manufacturer. – High speeds may need precision bearings. |
Size | Fit with shaft and housing dimensions. | – Confirm inner diameter (ID), outer diameter (OD), and width. – Ensure assembly compatibility. |
Precision | Accuracy of rotation required. | – Standard (P0/ABEC 1) for most uses. – P6/ABEC 5 or P5/ABEC 7 for high-speed/precision. |
Environment | Operating conditions like temperature, moisture, or contamination. | – High temp: Use heat-resistant materials or grease. – Moisture/dirt: Choose sealed (2RS) or shielded (2Z) bearings. – Corrosive: Consider stainless steel or ceramic. |
Misalignment | Tolerance for shaft and housing misalignment. | – Self-aligning bearings for misalignment (e.g., self-aligning ball or spherical roller bearings). – Rigid bearings (e.g., deep groove) require precise alignment. |
Lubrication | Type and maintenance of lubrication. | – Grease for low maintenance. – Oil for high speed or temperature. – Sealed bearings for pre-lubrication. |
Bearing Type | Specific designs for different applications. | – Deep groove: General-purpose, moderate loads. – Angular contact: High axial loads. – Thrust: Pure axial loads. – Roller bearings: High radial loads (e.g., cylindrical or tapered roller). |
Service Life | Expected operational lifespan. | – Calculate L10 life based on load and speed. – Consider maintenance and replacement feasibility. |
Cost & Availability | Budget and supply chain considerations. | – Balance performance with cost. – Ensure bearings are readily available. |
What types of loads can ball bearings handle? Radial, axial, or combined?
- Radial Loads: These are forces acting perpendicular (at a 90-degree angle) to the shaft. Think of the weight supported by the wheels on a cart. Most common ball bearings, like Deep Groove Ball Bearings, are excellent at handling radial loads. Self-Aligning Ball Bearings also primarily handle radial loads.
- Axial Loads (Thrust Loads): These are forces acting parallel to the shaft (pushing or pulling along its length). Imagine the force on a propeller shaft pushing a boat forward.
- Thrust Ball Bearings are specifically designed only for axial loads.
- Deep Groove Ball Bearings can handle some axial load in either direction, but not as much as dedicated thrust bearings.
- Angular Contact Ball Bearings are designed to handle axial loads in one specific direction (or both directions if used in pairs).
- Combined Loads: This is when both radial and axial loads are present at the same time. Angular Contact Ball Bearings are particularly good at handling combined loads. Deep Groove Ball Bearings can also handle moderate combined loads.
Deep groove ball bearings are common, what conditions are they suitable for?
- Versatile Loading: They handle primarily radial loads very well but can also take moderate axial loads in both directions. This makes them adaptable.
- Moderate to High Speeds: They can operate effectively at a wide range of speeds, including relatively high ones.
- General Purpose Applications: Because they are simple, reliable, and cost-effective, they are used almost everywhere – from small electric motors and power tools to car wheels and industrial gearboxes.
- Low Maintenance: When properly sealed and lubricated (often “sealed for life” in smaller sizes), they require minimal maintenance.
- Good Availability: They come in a huge variety of sizes and configurations (open, sealed, shielded).
What do ball bearing precision grades (e.g., P0, P6, P5) mean and how to choose?
- Precision grades define how accurately a bearing is manufactured, specifically relating to its dimensional and running tolerances. Think of it like the quality control standard. Common systems are ISO (P grades) and ABEC (used mainly in the US).
- What the Grades Mean (ISO Grades):
- P0 (or “Normal”): Standard precision. Suitable for the vast majority of general industrial and automotive applications. (Roughly equivalent to ABEC 1).
- P6: Increased precision over P0. Tighter tolerances for dimensions and running accuracy. (Roughly equivalent to ABEC 3).
- P5: High precision. Even tighter tolerances than P6. (Roughly equivalent to ABEC 5).
- P4, P2: Very high / ultra-high precision. Used for very demanding applications. (Roughly equivalent to ABEC 7, ABEC 9).
- How to Choose:
- For most applications (motors, gearboxes, wheels, general machinery): P0 (Normal) precision is perfectly adequate and the most cost-effective choice.
- Choose P6 or P5 if your application requires higher running accuracy, higher speeds, or lower noise/vibration levels (e.g., machine tool spindles, precision instruments, some electric motors).
- Choose P4 or P2 only for very specialized applications requiring extreme accuracy and speed (e.g., aerospace, high-frequency spindles).
- Keep in mind: Higher precision grades are significantly more expensive and often require more precise mounting practices and cleaner operating environments to realize their benefits.
What materials are ball bearings typically made of? What are the advantages of stainless steel or ceramic ball bearings?
- Standard Material: Most ball bearing rings (inner and outer races) and balls are made from a special type of high-carbon chromium bearing steel (like GCr15 in China or SAE 52100 in the US).
- Why? This steel offers an excellent combination of high hardness (resists wear and deformation), strength, durability, and relatively low cost. Cages are often made of stamped steel, brass, or polymer.
- Stainless Steel Bearings:
- Material: Typically made from martensitic stainless steel (like 440C).
- Advantages: The main advantage is corrosion resistance. They are ideal for environments where moisture, water, or mild chemicals are present.
- Applications: Food and beverage processing, medical equipment, marine applications.
- Trade-offs: Usually have slightly lower load capacity and hardness compared to standard chromium steel, and are more expensive.
- Ceramic Ball Bearings (Hybrid or Full Ceramic):
- Material: Balls are often made of Silicon Nitride (Si3N4) or Zirconia (ZrO2). Rings can be steel (making it a hybrid bearing) or also ceramic (full ceramic).
- Advantages:
- Higher Speed
- Lower Friction & Heat
- Increased Hardness & Stiffness
- Corrosion Resistance
- Electrical Insulation
- Less Lubrication Needed
- Applications: High-speed spindles, aerospace, racing, medical devices, vacuum environments, corrosive environments.
- Trade-offs: Significantly more expensive than steel bearings. Can be more brittle (sensitive to shock loads).
Do ball bearings need lubrication? How often should grease/oil be added?
- Yes, lubrication is essential! It reduces friction, prevents wear, removes heat, and protects against corrosion.
- Grease is most common and stays in place well. Oil is used for very high speeds or temperatures.
- Re-lubrication Frequency:
- Many smaller bearings are sealed and “lubricated for life” – they don’t need more grease under normal use.
- For others, follow the machine or bearing manufacturer’s recommendations. Frequency depends heavily on speed, load, temperature, and bearing type/size. There’s no single answer.
- Caution: Both too little and too much lubricant can cause problems (like overheating).
How to correctly install and remove ball bearings to avoid damage?
- Installation:
- Work clean. Keep bearing, shaft, and housing free of dirt.
- Use proper tools (press, sleeve kit, heater). Never hammer directly on the bearing.
- Apply force to the correct ring: Inner ring when pressing onto a shaft, Outer ring when pressing into a housing. Never push through the balls.
- Ensure it’s mounted straight.
- Removal:
- Use correct pullers.
- Pull on the ring being removed (inner ring off shaft, outer ring out of housing). Avoid pulling through the balls.
- Be careful not to damage the shaft or housing.
When in doubt, check the manual or ask an expert.
What causes ball bearing noise or overheating? How to troubleshoot?
- Lubrication Problems: Too little, too much, wrong type, old, or dirty lubricant. (Very common!)
- Contamination: Dirt or moisture inside the bearing.
- Bad Installation: Misalignment, fit too tight, damage during mounting.
- Bearing Damage: Wear, fatigue (flaking), corrosion.
- Overload/Overspeed: Running beyond limits.
- Wrong Bearing: Incorrect type/size chosen for the job.
- Troubleshooting:
- Check lubricant condition and level. Re-lube correctly if needed.
- Listen to the noise, check the temperature.
- Inspect seals for damage.
- Consider if operating conditions (load/speed) changed.
- If problem persists, the bearing likely needs replacement. Try to find the cause before installing a new one.
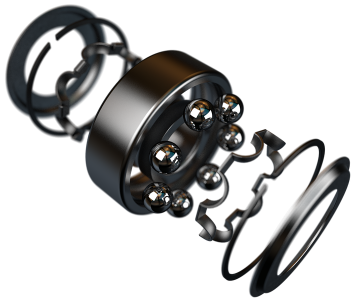
CAN’T FIND WHAT YOU NEED?
Please provide your question.
We’ll find you with the best support options.